Additive Manufacturing of Liquid Metal based Stretchable Electronics
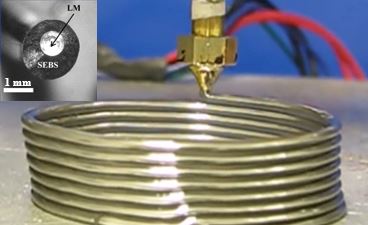
Flexible and stretchable electronics are emerging technology with myriad applications due to their ability to conform to complex with non-planar surfaces. Conventionally processed flexible electronic devices suffer from inherent rigidity and exhibit poor performance. Recently, liquid metals (LMs) have emerged as smart materials for electronics applications. Because they remain liquid at room temperature, LMs exhibit extreme stretchability and flexibility, if patterned and embedded in an elastomer matrix. The non-toxic eutectic alloy of gallium and indium (EGaIn) has been successfully used in many electronic applications because of its superior conductivity with virtually no vapor pressure, low viscosity, and compatibility in microchannels due to the instantly formed oxide skin. Most LM-based microfluidic electronic devices are usually fabricated using conventional expensive manual operations such as soft lithography and direct ink writing. These techniques are limited to 2D planar and quasi 3D (stacked 2D) devices with limited functionality. The ability to directly manufacture LM-based microfluidic devices has not been achieved yet. Therefore, we are designing a microfluidic-based multi-material extruder system with an integrated ultraviolet (UV) curing device and develop an AM system to print microwire (<50 μm) having a core of EGaIn and shell of UV cured elastomer. The team had previously developed a 3D printing system that demonstrated proof of concept by printing coarse resolution (~2 mm) extrudate of EGaIn core and thermoplastic elastomeric shell in a single process without the need for post-processing.
Multi-material 3D Printing of Chemically Immiscible Polymers
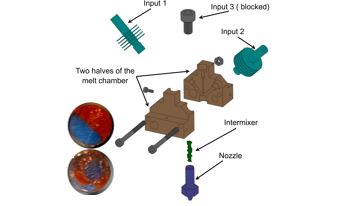
Fused deposition modeling (FDM) printers are some of the most common additive manufacturing (AM) systems in use today. One of their most significant drawbacks compared with alternative AM techniques is that they are unable to easily integrate multiple materials into a single process to produce gradient parts, which have different mechanical properties within a single printed object. Much of this limitation comes from the need to have single filaments as inputs to a printed part, and weak bonding between thermoplastics if they are not chemically miscible. We have designed an extruder system with a static intermixer to actively enhance the bonding strength between chemically immiscible thermoplastics for a multi-input FDM system. This system was successfully used to enhance adhesion between rigid and soft, stretchable polymers, which have nearly three orders of magnitude of difference in elastic moduli. The replaceable intermixer within the print head permits direct comparison of side-by-side or intermixed coextrusion processes. The bond strength between adjacent deposited fibers in intermixed printing was found to be at least 12 times higher than that of the fibers in side-by-side printing. As a proof-of-concept, tendon-driven soft robotic fingers with functionally gradient materials produced from mechanically interlocked dissimilar polymers have been printed and characterized. The fingers printed with intermixed coextrusion of hard and soft polymers do not show any noticeable interface failure after 10,000 cycles of operation, whereas other samples printed with side-by-side coextrusion experienced layer delamination before 10,000 cycles.
3D Printing of Structural Components using Lunar Regolith

Instead of just short-term visits, space exploration is now well-positioned in exploring ways to build habitats for astronauts on Moon and other nearby planets. Due to the economic challenges with transporting building materials from Earth, is-situ resource utilization (ISRU) of lunar regolith as a raw material for architectural habitats and other structural components or spare parts has gained significant interest in recent years. Lunar regolith, also known as lunar soil, has the potential as lunar construction material, mainly because of its abundance on the Moon surface, thermal stability, and radiation shielding properties. Lunar regolith is a powdered material with a wide size range of particles ranging from ~ 50 µm to ~1000 µm and it contains heavy metals with many minerals found on Earth. Additive manufacturing (AM) has the potential to be used in Moon to print 3D parts using the lunar regolith. The direct-write technique, extrusion AM coupled with a robotic system can be utilized in printing components in Moon, without restricting to a maximum build volume and requiring a laser safety system and powder delivery unit. The goal of this research program is to design and characterize a multi-functional lunar regolith/vitrimer epoxy-based composite suitable for extrusion AM to print regolith structures with enhanced mechanical properties. The project also involves developing the extruder system and the controlled build volume for the extrusion AM technology under lunar conditions.
Innovative Design for Additive Manufactruing (DfAM)

Additive manufacturing (AM) has evolved as one of the core component of the fourth industrial revolution, Industry 4.0. This is mainly becuase it offers users free form design space, hence manufacturing very complex parts as a single component is now possible with the power of AM. Therefore, many industries like aerospace, automobile, biomedical and others are increasignly investing in adoption of AM. AM supports manufacturing of light-weight, efficient product design with enhanced functionality. The flexibility offered by AM enables generative design techniques like topology optimization (TO). In TO, finite element analysis is used to optimize the distribution of masses and voids in a predefined design space so that the final design structure meets all the prescribed loading and boundary conditions. However, the objective of design for AM (DfAM) does not end with only designing organic forms that mimic efficient natural structures, but also include intellegent design optimization to ensure the parts are self-supporting requiring minimal amount of support structures. Under this reseach stream, we utilize commercial software such as nTopology, Gen3D and Fusion 360 to optimize design of heat exchangers, brackets, consolidated parts with improved performance. We focus on both polymer and metal AM techniques with different guidelines for DfAM.